The Importance of Double Welded Pipes and Polyurethane Lined Pipes in Pipe Welding
Double welded pipe refers to pipe that has been double welded to create a stronger, more durable joint. This type of pipe is commonly used in pipeline construction where welding quality and strength are critical. The double welding process involves using welding techniques to fuse two separate pipes together to ensure a strong and seamless connection. Not only does this enhance the overall strength and durability of the pipe, it also reduces the risk of welding defects and potential leaks.
Polyurethane lined pipe, on the other hand, is a pipe lined with a polyurethane coating that provides additional protection against corrosion, abrasion, and chemical attack. The lining is applied to the inside surface of the pipe to create a barrier between the fluid being transported and the metal surface of the pipe. Polyurethane lined pipes are particularly beneficial for pipes used to carry corrosive substances or operate in harsh environmental conditions. Polyurethane linings not only extend the life of your pipes, they also minimize the risk of leaks and maintenance costs.
Mechanical Property
Grade 1 | Grade 2 | Grade 3 | |
Yield Point or yield strength, min, Mpa(PSI) | 205(30 000) | 240(35 000) | 310(45 000) |
Tensile strength, min, Mpa(PSI) | 345(50 000) | 415(60 000) | 455(66 0000) |
In addition, the production efficiency of spiral steel pipes is significantly higher than that of seamless steel pipes. For seamless pipe, the production process involves extruding a solid steel billet through a perforated rod, resulting in a relatively slower and more complex production process. In contrast, spiral welded pipe can be manufactured in larger diameters and lengths, resulting in shorter production times and increased efficiency. This ensures a consistent supply of high-quality pipes in shorter time periods, making it a reliable and time-saving solution for various industries.
Another noteworthy advantage of spiral welded pipes is their excellent resistance to external pressure and mechanical stress. Welds provide additional durability, allowing these pipes to withstand higher pressures than seamless pipes. This property is particularly important for applications in the oil and gas industry, where pipelines are subject to significant internal and external pressures. By using spiral welded pipes, companies can ensure the safe and efficient transportation of these important resources.
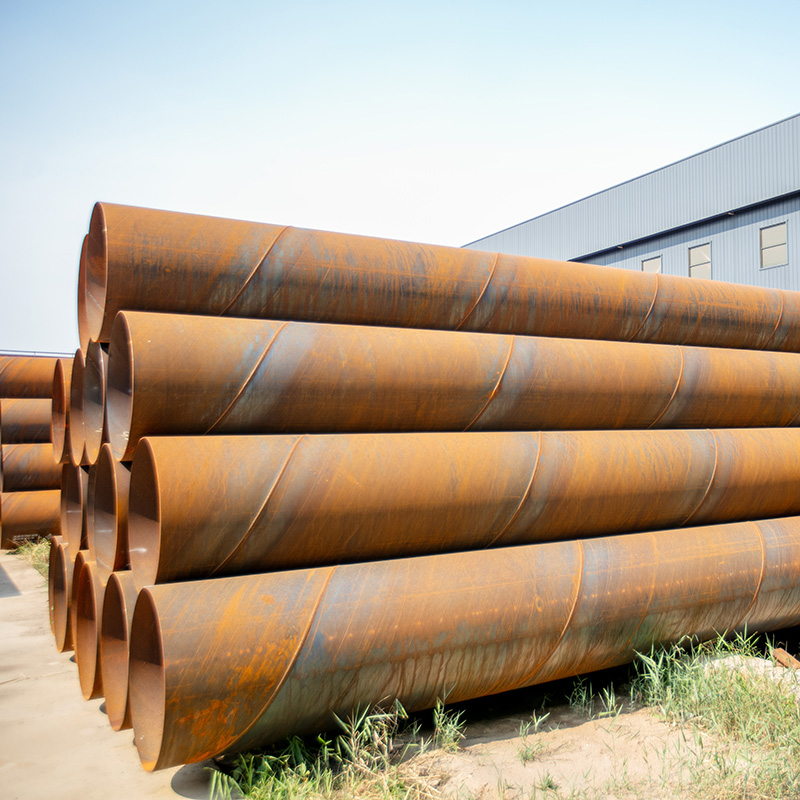
In pipe welding, the combination of double welded pipe and polyurethane lined pipe offers many advantages. First and foremost, the use of double-welded pipe ensures the structural integrity of the pipe, reducing the possibility of welding defects and subsequent failure. This is particularly important in industrial environments where pipes are subject to high pressures and temperature fluctuations. Additionally, the use of polyurethane-lined pipes provides an additional layer of protection against corrosion and wear, further increasing the pipe’s durability and lifespan.
In addition, the use of double-welded pipe and polyurethane-lined pipe can provide cost savings to pipeline operators. The enhanced strength and durability of double welded pipe can reduce the need for frequent repairs and maintenance, saving time and money in the long run. Likewise, the protective coating provided by polyurethane-lined pipe can extend the service life of the pipe, thereby reducing replacement and repair costs.
In conclusion, the use of double welded pipes and polyurethane lined pipes is crucial in pipe welding. These components not only ensure the structural integrity and strength of the pipeline, but also provide necessary protection against corrosion, abrasion and chemical attack. By incorporating these advanced technologies into pipeline construction, operators can achieve higher levels of reliability, performance and cost-effectiveness for their pipeline systems.