Spiral Submerged Arc Welding In Oil Pipe Line Construction: Ensuring Service Life And Reliability
Learn about HSAW:
Spiral submerged arc welding is an advanced welding technology that combines the principles of submerged arc welding and spiral tube forming. It involves using an automated welding process to create a continuous spiral weld by feeding a solid filler wire into a flux-covered arc. This method ensures consistent and high-quality welds, eliminating the risk of defects common with other welding methods.
applications.
Mechanical Property
steel grade |
minimum yield strength |
Tensile strength |
Minimum elongation |
Minimum impact energy |
||||
Specified thickness |
Specified thickness |
Specified thickness |
at test temperature of |
|||||
<16 |
>16≤40 |
<3 |
≥3≤40 |
≤40 |
-20℃ |
0℃ |
20℃ |
|
S235JRH |
235 |
225 |
360-510 |
360-510 |
24 |
- |
- |
27 |
S275J0H |
275 |
265 |
430-580 |
410-560 |
20 |
- |
27 |
- |
S275J2H |
27 |
- |
- |
|||||
S355J0H |
365 |
345 |
510-680 |
470-630 |
20 |
- |
27 |
- |
S355J2H |
27 |
- |
- |
|||||
S355K2H |
40 |
- |
- |
The importance of HSAW in oil pipeline construction:
1. Strength and Durability: One of the primary attributes of HSAW is its ability to form strong, high-strength welded joints. The continuous spiral weld formed by this technology enhances the structural integrity and is critical to withstand the high pressures, extreme temperatures and environmental factors that oil pipe lines face during their service life.
2. Long life and strong reliability: Oil pipe lines are expected to operate flawlessly for decades, transporting oil without leakage or failure. HSAW plays a vital role in achieving long service life by ensuring even distribution of welding heat, minimizing stress concentrations, and preventing crack initiation and propagation - all factors that contribute to the overall reliability of the pipe.
3. Efficient construction: HSAW is capable of continuously welding long sections of pipeline, so it has significant efficiency in pipeline construction. This method reduces welding time, increases productivity, significantly reduces construction costs, and is conducive to the timely completion of the project.
4. Reduced maintenance and repairs: By providing high-quality, defect-free welds, HSAW minimizes the need for future repairs or maintenance-related downtime. Oil pipelines built using this method are less prone to leaks or failures, improving safety and increasing operational efficiency.
5. Environmental benefits: HSAW ensures the production of precision welds with high dimensional accuracy. This reduces the likelihood of pipeline corrosion and subsequent oil leakage, protecting the environment from potential disasters associated with pipeline failure.
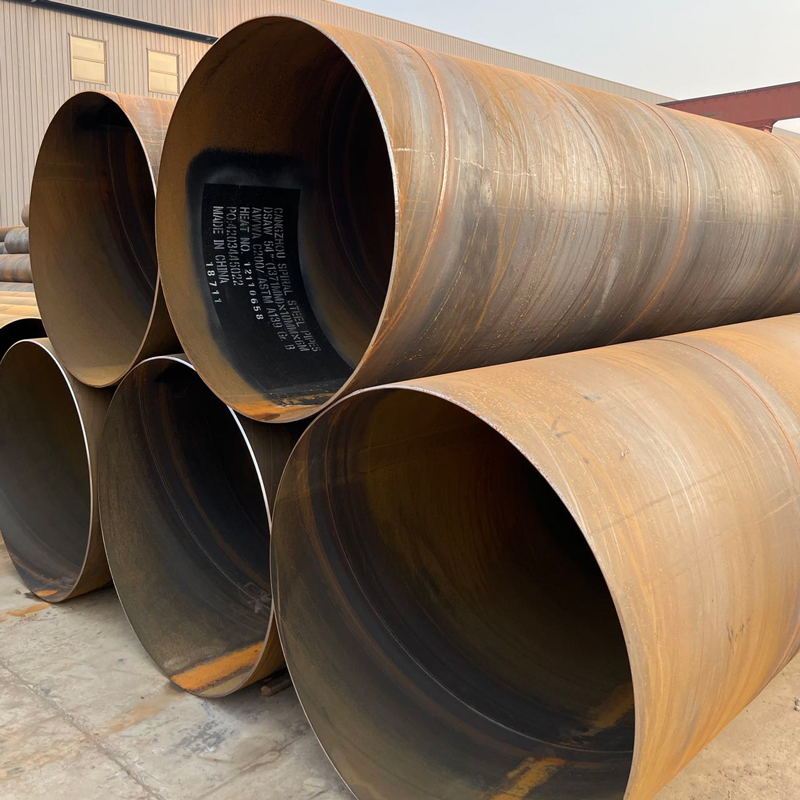
Chemical Composition
Steel grade |
Type of de-oxidation a |
% by mass, maximum |
||||||
Steel name |
Steel number |
C |
C |
Si |
Mn |
P |
S |
Nb |
S235JRH |
1.0039 |
FF |
0,17 |
— |
1,40 |
0,040 |
0,040 |
0.009 |
S275J0H |
1.0149 |
FF |
0,20 |
— |
1,50 |
0,035 |
0,035 |
0,009 |
S275J2H |
1.0138 |
FF |
0,20 |
— |
1,50 |
0,030 |
0,030 |
— |
S355J0H |
1.0547 |
FF |
0,22 |
0,55 |
1,60 |
0,035 |
0,035 |
0,009 |
S355J2H |
1.0576 |
FF |
0,22 |
0,55 |
1,60 |
0,030 |
0,030 |
— |
S355K2H |
1.0512 |
FF |
0,22 |
0,55 |
1,60 |
0,030 |
0,030 |
— |
a. The deoxidation method is designated as follows: FF: Fully killed steel containing nitrogen binding elements in amounts sufficient to bind available nitrogen (e.g. min. 0,020 % total Al or 0,015 % soluble Al). b. The maximum value for nitrogen does not apply if the chemical composition shows a minimum total Al content of 0,020 % with a minimum Al/N ratio of 2:1, or if sufficient other N-binding elements are present. The N-binding elements shall be recorded in the Inspection Document. |
In conclusion:
The construction of oil pipelines requires the highest welding standards to ensure longevity, reliability and safety. Spiral submerged arc welding (HSAW) is the proven technology of choice in this field due to its ability to form strong, durable and defect-free welds. With numerous advantages including enhanced structural integrity, efficient construction, reduced maintenance and environmental benefits, HSAW plays a key role in meeting global oil transportation needs. As the oil industry continues to expand, the use of advanced welding technologies such as HSAW is critical to maintaining the integrity and reliability of oil pipelines around the world.

In summary
Cangzhou Spiral Steel Pipe Group Co., Ltd. is proud to provide high-quality spiral seam pipes for a variety of applications. We focus on precision manufacturing, advanced welding technology and quality materials to provide customers with reliable, efficient solutions for their piping needs. Trust us to meet all your requirements and experience first-hand the reliability and resilience of our spiral seam pipes.