Mastering Pipe Welding Procedures: A Comprehensive Guide
1. Understand the basics of pipe welding procedures
Pipe welding involves joining sections of pipes together to form a continuous and leak-proof pipe. The process requires a thorough understanding of welding techniques such as TIG (tungsten inert gas), MIG (metal inert gas) and stick welding. Each technology has its own advantages and limitations, and the choice of technology depends on factors such as material type, pipe diameter and welding location.
Standardization Code | API | ASTM | BS | DIN | GB/T | JIS | ISO | YB | SY/T | SNV |
Serial Number of Standard |
A53 |
1387 |
1626 |
3091 |
3442 |
599 |
4028 |
5037 |
OS-F101 | |
5L | A120 |
102019 |
9711 PSL1 |
3444 |
3181.1 |
5040 |
||||
A135 | 9711 PSL2 |
3452 |
3183.2 |
|||||||
A252 |
14291 |
3454 |
||||||||
A500 |
13793 |
3466 |
||||||||
A589 |
2. Pipe welding preparation
Adequate preparation is crucial before starting the welding process. This includes cleaning the surfaces to be welded, ensuring the pipes are installed correctly and selecting the appropriate welding materials. Additionally, it is crucial to follow safety protocols and ensure that the work area is free of any potential hazards.
3. Choose the right equipment
The selection of welding equipment plays a vital role in the success of your pipe welding program. This includes selecting the appropriate welding machine, welding electrodes, shielding gases and other accessories. It is important to invest in high-quality equipment to ensure the integrity of the welds and the entire piping system.
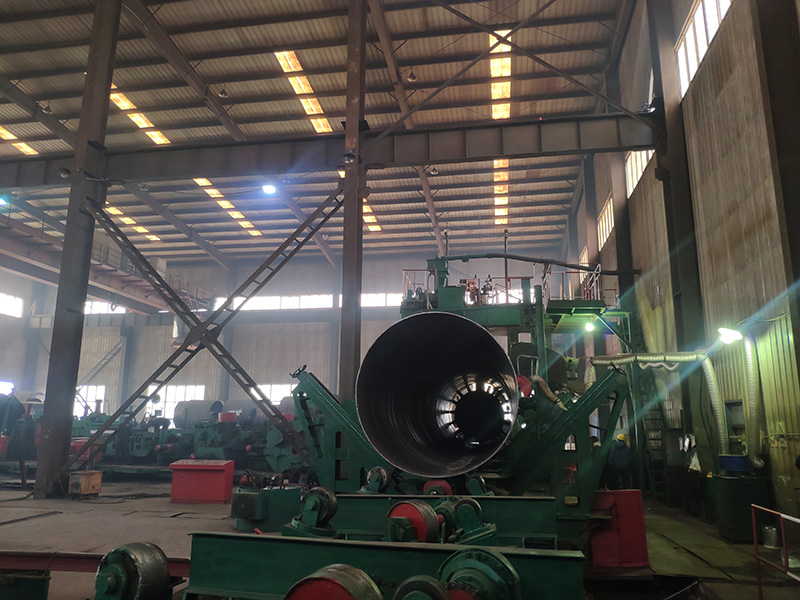
4. Implement best practices
Adherence to best practices is critical to achieving high-quality and durable pipe welding. This includes maintaining the correct welding parameters such as voltage, current and travel speed to ensure proper penetration and fusion. Additionally, proper joint preparation, including bevel and edge preparation, is critical to achieving a strong and reliable weld.
5. Ensure Code Compliance
In many industries, pipe welding procedures must adhere to specific codes and standards to ensure the integrity and safety of the piping system. This may include compliance with specifications such as ASME B31.3, API 1104, or AWS D1.1. Welders and welding inspectors must have a thorough understanding of these specifications and ensure that all welding procedures meet the required standards.
6. Quality control and inspection
Quality control and inspection are integral parts of the pipe welding program. This includes performing visual inspections, non-destructive testing (NDT) and destructive testing to ensure the quality and integrity of the welds. Welding inspectors play a vital role in verifying that welding processes comply with specified requirements and standards.
In summary, mastering pipe welding procedures requires a combination of technical expertise, proper equipment, adherence to best practices, and compliance with industry standards. By following these guidelines, welders can ensure the reliability and safety of piping systems in a variety of industrial applications. Continuous training and awareness of the latest advances in welding technology are also critical to mastering pipe welding procedures and achieving excellence in the field.
