Spiral Welded Tube Arc Welding Of Natural Gas Pipes
For natural gas pipes, safety and reliability are paramount. Arc welding plays a vital role in ensuring that these pipes can withstand the harsh conditions they face during their service life. The arc welding process involves using electricity to generate intense heat that melts the edges of pipes and fuses them together.
Standard |
Steel grade |
Chemical composition |
Tensile properties |
Charpy Impact Test and Drop Weight Tear Test |
||||||||||||||
C | Si | Mn | P | S | V | Nb | Ti | CEV4)(%) | Rt0.5 Mpa Yield strength | Rm Mpa Tensile Strength | Rt0.5/ Rm | (L0=5.65 √ S0 )Elongation A% | ||||||
max | max | max | max | max | max | max | max | Other | max | min | max | min | max | max | min | |||
L245MB |
0.22 |
0.45 |
1.2 |
0.025 |
0.15 |
0.05 |
0.05 |
0.04 |
1) |
0.4 |
245 |
450 |
415 |
760 |
0.93 |
22 |
Charpy impact test: Impact absorbing energy of pipe body and weld seam shall be tested as required in the original standard. For details, see the original standard. Drop weight tear test: Optional shearing area |
|
GB/T9711-2011(PSL2) |
L290MB |
0.22 |
0.45 |
1.3 |
0.025 |
0.015 |
0.05 |
0.05 |
0.04 |
1) |
0.4 |
290 |
495 |
415 |
21 |
|||
L320MB |
0.22 |
0.45 |
1.3 |
0.025 |
0.015 |
0.05 |
0.05 |
0.04 |
1) |
0.41 |
320 |
500 |
430 |
21 |
||||
L360MB |
0.22 |
0.45 |
1.4 |
0.025 |
0.015 |
1) |
0.41 |
360 |
530 |
460 |
20 |
|||||||
L390MB |
0.22 |
0.45 |
1.4 |
0.025 |
0.15 |
1) |
0.41 |
390 |
545 |
490 |
20 |
|||||||
L415MB |
0.12 |
0.45 |
1.6 |
0.025 |
0.015 |
1)2)3 |
0.42 |
415 |
565 |
520 |
18 |
|||||||
L450MB |
0.12 |
0.45 |
1.6 |
0.025 |
0.015 |
1)2)3 |
0.43 |
450 |
600 |
535 |
18 |
|||||||
L485MB |
0.12 |
0.45 |
1.7 |
0.025 |
0.015 |
1)2)3 |
0.43 |
485 |
635 |
570 |
18 |
|||||||
L555MB |
0.12 |
0.45 |
1.85 |
0.025 |
0.015 |
1)2)3 | Negotiation |
555 |
705 |
625 |
825 |
0.95 |
18 |
|||||
Note: | ||||||||||||||||||
1)0.015 ≤ Altot < 0.060;N ≤ 0.012;AI—N ≥ 2—1;Cu ≤ 0.25;Ni ≤ 0.30;Cr ≤ 0.30;Mo ≤ 0.10 | ||||||||||||||||||
2)V+Nb+Ti ≤ 0.015% | ||||||||||||||||||
3)For all steel grades, Mo may ≤ 0.35%, under a contract. | ||||||||||||||||||
4)CEV=C+ Mn/6 + (Cr+Mo+V)/5 + (Cu+Ni)/5 |
One of the key factors to consider when arc welding natural gas pipes is the type of welding technique used. For spiral welded tubes, the most commonly used method is submerged arc welding (SAW) technology. This involves using granular flux, which is poured over the welding area to create a protective atmosphere that prevents oxidation and other contaminants from affecting the weld. This results in a high-quality, uniform weld with minimal defects.
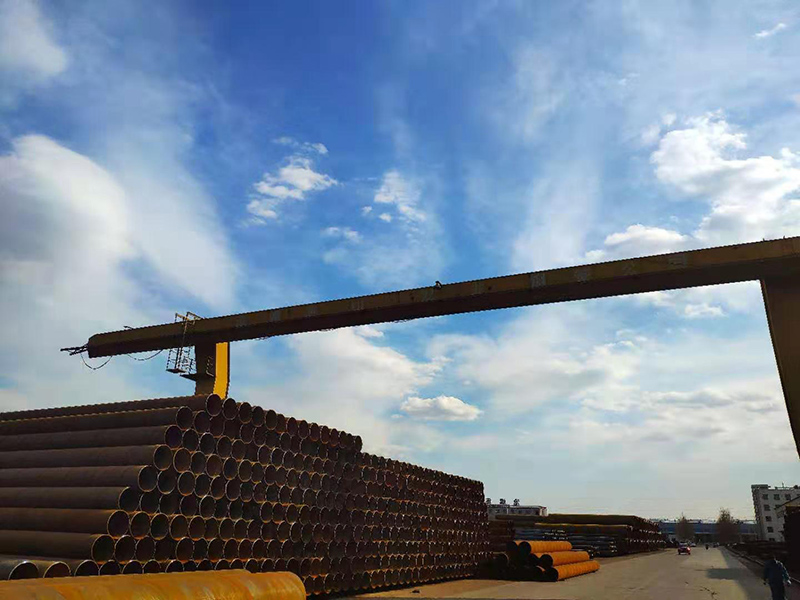
Another important consideration when arc welding natural gas pipes is the selection of weld filler material. Filler material is used to fill any gaps or irregularities in the weld, creating a strong and consistent bond. For spiral welded pipes, a filler material must be used that is compatible with the specific steel grade used and the environmental conditions to which the pipeline is exposed. This ensures that the weld can withstand the pressures and temperatures experienced by natural gas pipes.
In addition to the technical aspects of arc welding, it is also important to consider the qualifications and experience of the welder performing the work. Arc welding of natural gas pipes requires a high level of skill and expertise, as well as a thorough understanding of the unique challenges and requirements of the job. It’s critical to work with experienced and certified welders who can consistently produce high-quality welds that meet the industry’s rigorous standards.
In conclusion, spiral welded tube arc welded natural gas pipe is a key component of the pipeline industry. It requires careful consideration of welding techniques, filler materials, and the qualifications of the welder performing the work. By ensuring these factors receive the attention they deserve, it will be possible to create natural gas pipes that meet the industry's requirements for safety, reliability and long-term performance.