Hollow-Section Structural Pipes And Their Role In Oil Pipeline Infrastructure
Learn about hollow section structural pipes:
Hollow-section structural pipes, including spiral submerged arc welded pipes, are widely used in the oil and gas industry due to their superior strength and durability. These pipes are manufactured using submerged arc welding technology, where a welding arc is formed beneath a thick layer of granular flux. The process ensures that the molten weld seam and base material are protected from atmospheric contamination, resulting in a seamless and strong pipe structure.
Mechanical Property
Grade 1 | Grade 2 | Grade 3 | |
Yield Point or yield strength, min, Mpa(PSI) | 205(30 000) | 240(35 000) | 310(45 000) |
Tensile strength, min, Mpa(PSI) | 345(50 000) | 415(60 000) | 455(66 0000) |
The role of hollow cross-section structural pipes in oil pipe lines:
1. Enhance structural stability: Hollow-section structural pipes have high torsion resistance and are very suitable for long-distance pipeline transportation. Its sturdy construction enables seamless flow and minimizes the risk of leaks, ensuring the integrity of the oil pipe line system.
2. Corrosion Protection: The petroleum industry frequently exposes pipelines to corrosive internal and external corrosive agents. Hollow-section structural pipes can be coated with corrosion-resistant materials to provide long-lasting protection against rust, chemicals and other deteriorating factors. This allows oil pipelines to operate efficiently for long periods of time.
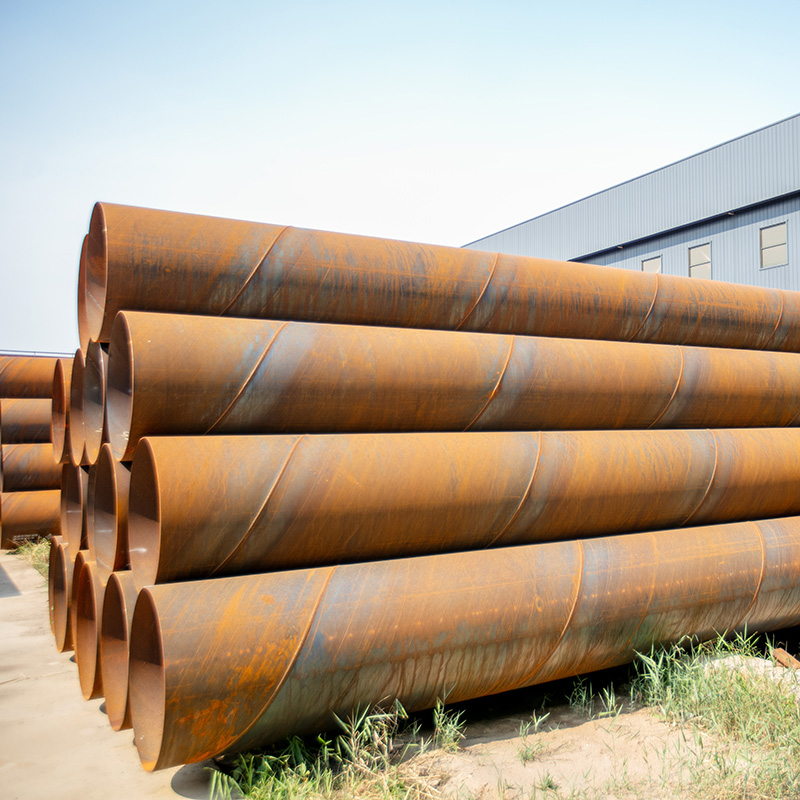
3. Versatility in terrain adaptation: Oil pipe line routes often traverse complex terrain, including mountains, valleys, and underwater obstacles. Hollow-section structural pipes are designed in a variety of diameters and wall thicknesses, allowing the flexibility to adapt to varying terrains without compromising structural integrity. They can effectively withstand external pressure and geological stress, ensuring the safety and reliability of the oil transportation system.
4. Cost-Effectiveness: Hollow-section structural pipes are generally more cost-effective than other piping options such as solid steel pipes due to their greater material efficiency. The welding process allows for the creation of larger diameter pipes, thereby reducing the need for excessive joint connections. Additionally, their strength-to-weight ratio ensures optimal material utilization and reduces transportation costs.
5. Ease of maintenance and repair: Hollow section structural pipes are usually designed with ease of maintenance and repair in mind. If damage or wear occurs, individual pipes can be replaced without the need to extensively dismantle the entire pipe. This approach minimizes downtime and reduces repair costs, ensuring continuous oil flow.
In conclusion:
Hollow section structural pipes, especially SSAW pipes, play a vital role in building durable and efficient oil pipe line networks. These pipelines have become the preferred choice of the oil and gas industry due to their enhanced structural stability, corrosion protection, adaptability to different terrains, cost-effectiveness and ease of maintenance. The critical role they play in ensuring the safe and reliable transportation of oil cannot be overstated. The continued development and utilization of hollow profile structural pipes will further enhance oil pipe line infrastructure to meet the growing energy needs of today's world.