The Importance Of Spiral Welded Pipes For Underground Natural Gas Pipelines
Evolution of welded pipe and spiral welding technology:
Welded tubes play a vital role in modern engineering and construction. Over the years, different welding methods have been developed, each with its own unique advantages. Among these technologies, spiral welding is popular for its ability to produce high-quality welded tubes with superior strength and integrity. Spiral welded pipe is manufactured by continuously rolling a steel strip through a series of rollers to form a spiral shape. The edges of the strips are then welded together to create a strong and leak-proof pipe.
Mechanical Property
Grade 1 | Grade 2 | Grade 3 | |
Yield Point or yield strength, min, Mpa(PSI) | 205(30 000) | 240(35 000) | 310(45 000) |
Tensile strength, min, Mpa(PSI) | 345(50 000) | 415(60 000) | 455(66 0000) |
Advantages of spiral welded pipe:
1. Increased strength and durability: Compared to straight seam or straight seam welded pipes, spiral welded pipes exhibit significant strength due to the continuous spiral weld seam. Continuous welds enhance the pipe's ability to withstand high internal and external pressures, making it ideal for underground gas lines.
2. Resistance to stress and corrosion: Underground gas line networks are often subject to various stresses due to soil movement, temperature changes and external loads. Spiral welded pipes are elastic and offer excellent resistance to these stresses, reducing the risk of damage or failure. Additionally, these pipes can be coated with a protective coating to further enhance their corrosion resistance, ensuring a longer service life.
3. Enhanced flexibility: Spiral welded pipe is inherently flexible due to its spiral shape, allowing it to adapt to various terrains and installation conditions. This flexibility ensures pipelines are less susceptible to ground subsidence or shifting, providing a more reliable gas distribution network.
4. Cost-effectiveness: The manufacturing process of spiral welded pipes is highly efficient, thus saving costs. These pipes are available in longer lengths, reducing the number of joints required for installation. Fewer joints not only simplify the construction process, but also help improve the overall integrity of underground natural gas pipelines, minimizing the possibility of leaks or failures.
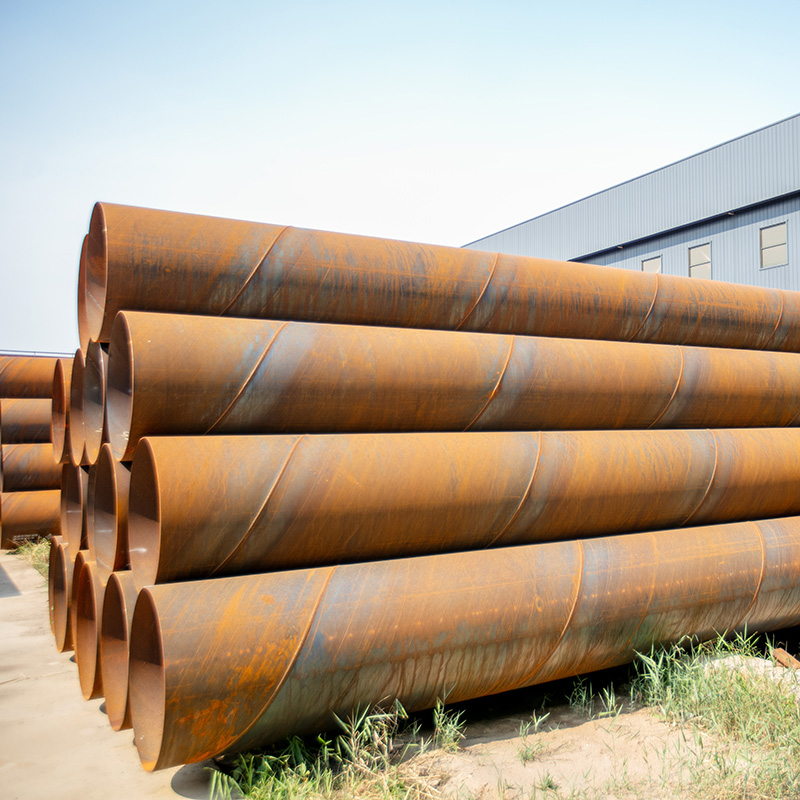
In conclusion:
As demand for natural gas continues to grow, reliable and efficient distribution methods are critical, especially for underground natural gas pipelines. Spiral welded pipes have proven to be the ideal solution, combining strength, durability, stress and corrosion resistance, flexibility and cost-effectiveness. By investing in high-quality spiral welded pipe, natural gas distribution companies can build a strong infrastructure that ensures a safe and uninterrupted supply of natural gas to communities, contributing to their growth and development.